The Future of Metal Fabrication: Latest Technology & Trends
Professional metal handling is essential for a wide range of industries, where this versatile material is used to create tools, technologies and infrastructure of all kinds. For instance, metals are integral to agricultural, electrical and automotive industries, meaning that these raw materials make a big contribution to the economy on a daily basis.
In particular, specialist skills and expertise are required to carry out metal fabrication work, where this involves the welding and assembling of raw materials to create new structures. As manufacturing methods develop, this process has become increasingly streamlined and cost effective, helping to boost productivity as well as sustainability.
Read on to find out more about recent developments in the world of metal fabrication, with a look at the latest technologies and trends that are driving the industry today.
What Is Metal Fabrication?
Metal fabrication describes the process of manipulating materials in order to create new parts, machinery and structures. Raw materials are cut, bent and welded to assemble essential pieces of infrastructure, where this is typically achieved with the help of specialist tools operated by skilled workers.
Many industries rely on this kind of precision manufacturing. Most notably, the automotive world relies on metal fabrication for the creation of specialist parts, including engines, exhaust systems and body panels.
Industrial operations rely on metal fabrication for the assembly of essential components such as conveyor belt systems and hard wearing manufacturing tools. In addition to this, metal work can also be more decorative in nature, with the assembly of gates, staircases, bridges and other architectural elements.
An Insight Into The Metal Fabrication Process
Metal fabrication is commonly used for the manufacture of automotive components, where these must be safe and hard wearing to meet strict industry standards. The process involved will vary depending on the project at hand, but some key steps can be traced across various fabrication jobs.
The fabrication process typically begins with detailed design work, where computer software may be utilised to ensure that all plans are precise and suitable. Once this initial stage is complete, the manufacturing work can begin. Raw sheets of metal or large bars will be cut down to the required size, where this is usually completed with the help of specialist machinery.
These metal pieces are then shaped using rollers, stamps or presses. Some projects will be entirely automated at this stage, whilst others will rely on manual interventions. Next, welding will take place to join distinct components together, helping the final product to take shape.
Once the component has been assembled, finishing touches can be applied. This typically involves polishing and cleaning, as well as the application of protective coatings and paints. The product will then undergo quality control testing before being packaged and shipped.
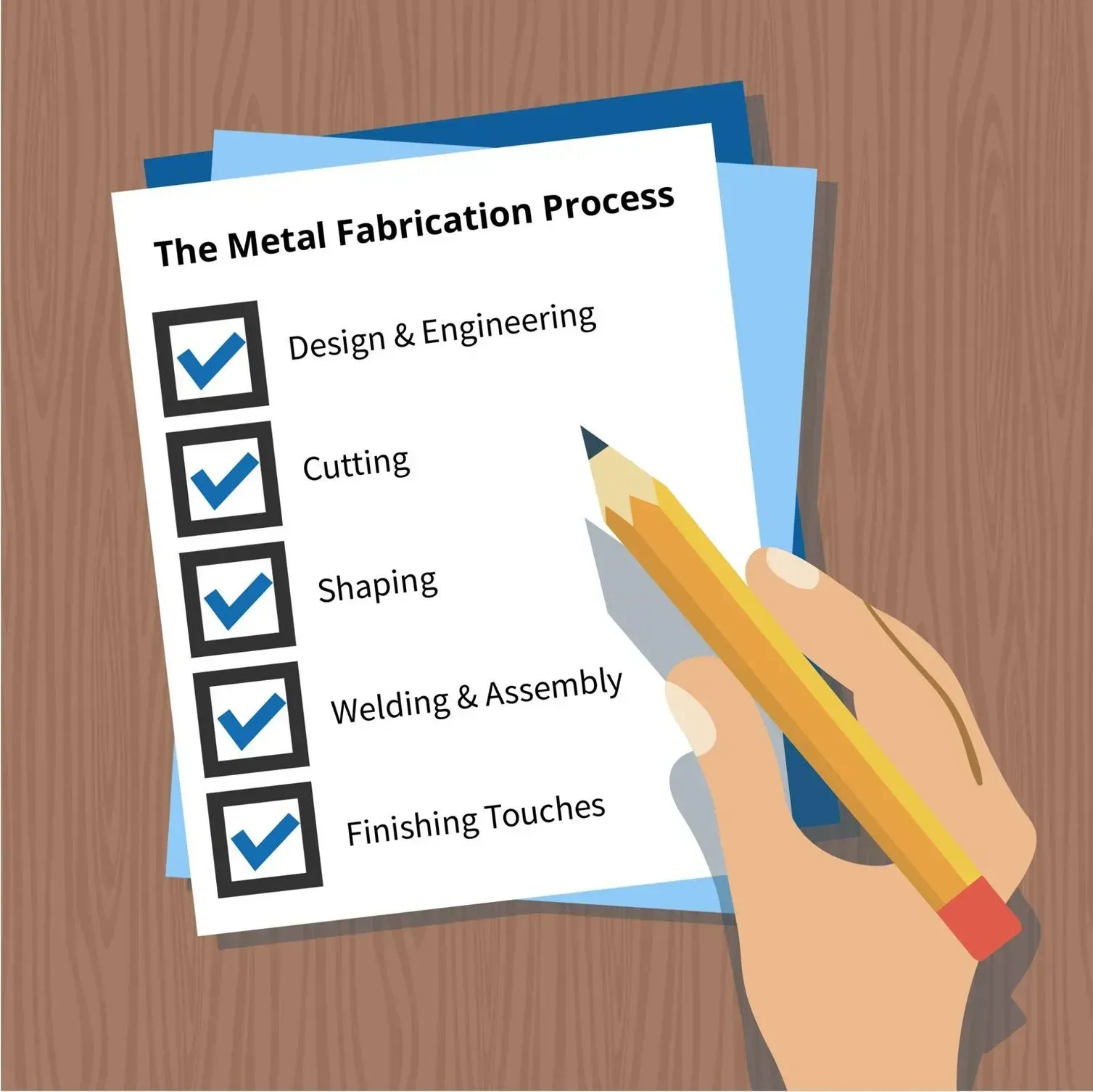
Metal Fabrication & New Technologies
As with all essential manufacturing industries, metal fabrication has changed drastically since its inception. Previously, metal handlers would be fully dependent on manual efforts to create new components, with all design work being carried out by hand.
Today, new technologies have been implemented to make this process safer, quicker and more efficient. This has transformed everything from the design stage to assembly, allowing more parts to be manufactured at a greater pace than ever before.
Some of these developments include:
Automation & Robotics
Previously, robotics and automated machinery was used for only the most difficult of tasks. Now however, this is becoming the norm, where many facilities complete all kinds of metal fabrication work in tandem with robots. These automated systems can speed up production and deal with labour shortages, helping to reduce costs across the production line.
3D Printing
Also known as additive manufacturing, 3D printing has increasingly become a part of the metal fabrication world. There are a number of different methods used to create metal parts in this way, including powder bed fusion, which allows for the printing of intricate designs with minimal waste. Usually, 3D printing involves depositing materials layer by layer, where the entire process is controlled by the computer.
Computer Aided Design
Additionally, computers can be used at the design stage. This technology has been used for decades by leading manufacturers, in order to tackle more complex projects, but today the majority of metal fabrication and design work is digital.
In particular, Computer-Aided Design (CAD) software is becoming increasingly popular, where these can allow designers to test components before fabrication commences. This kind of software also helps with the programming of Computer Numerical Control machines, which are used for cutting out intricate designs with precision.
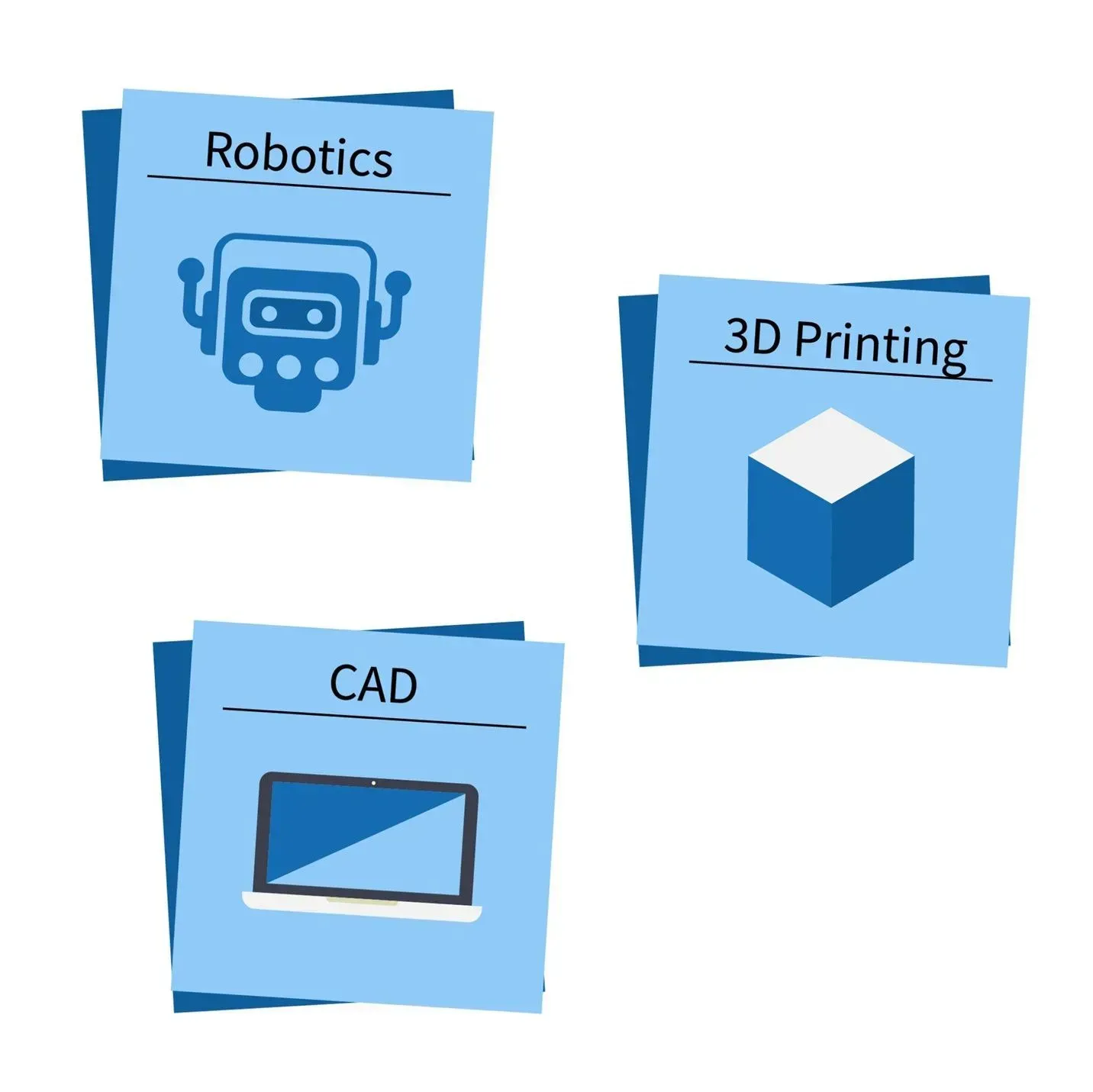
Sustainable Metal Manufacturing
Emerging trends in the metal manufacturing industry also relate to sustainable initiatives, where most manufacturing facilities are now looking to minimise their environmental impact across their production line.
Metal fabrication has changed in recent years to reflect these concerns, where overhauls of waste management practices and energy consumption are resulting in greener manufacturing strategies.
Some of these sustainability initiatives include:
Recycling & Reuse
As with many manufacturing industries, metal fabrication works can benefit from an increased focus on recycling. Raw material handling tends to use up a lot of energy through the extraction and transportation process, where the reuse of waste goes a long way to reducing the carbon footprint of a project.
Sustainable Finishes
Some traditional metal finishes, sealants and paints contain volatile organic compounds, or VOCS, where these can contribute to air pollution. To tackle this, metal fabrication facilities are making commitments to use non-toxic and water based products instead, which tend to be less environmentally harmful.
Energy Efficiency
Initiatives that focus on energy efficiency are also gaining in popularity in the metal fabrication world. This can mean upgrading old machinery for modern, energy saving alternatives, where some facilities are also looking to incorporate renewable energy sources into their power supply. This is a great way to cut overheads whilst also contributing to sustainable manufacturing efforts.
New Metal Alloys
Although most commonly used materials have been staples of the metal fabrication industry for centuries, new innovations are always welcome. Lightweight metal alloys are particularly favoured in the automotive industry for instance, where these help with the development of faster and more fuel efficient vehicles.
In a study published in 2024, a team of scientists at the Lawrence Berkeley National Laboratory unveiled a new kind of metal alloy that appeared to be more hard wearing than previously manufactured materials. The alloy was composed of niobium, tantalum, titanium, and hafnium, where it seemed to be resilient to both very hot and very cold temperatures.
The material was resistant to cracking under extreme temperatures due to a bending of crystals in the alloy at an atomic level. Scientists hope that with further testing, this metal could be used to build high efficiency engines or even the next generation of space travel equipment in the near future.
Developments like this represent the future of the metal fabrication industry, which is always looking for smarter ways to build essential components.
Cotmor Tool and Presswork: The Metal Fabrication Experts
As a leading metal pressing manufacturer, we offer a variety of specialist material handling services, including metal stamping, welding and fabrication.
We always use the latest presswork tools and technologies to ensure our clients are receiving top quality components, where we support a range of automotive suppliers and electrical engineers.
Get in touch with us today to find out more about our full range of services.