Spot Welding vs MIG Welding: Understanding the Differences
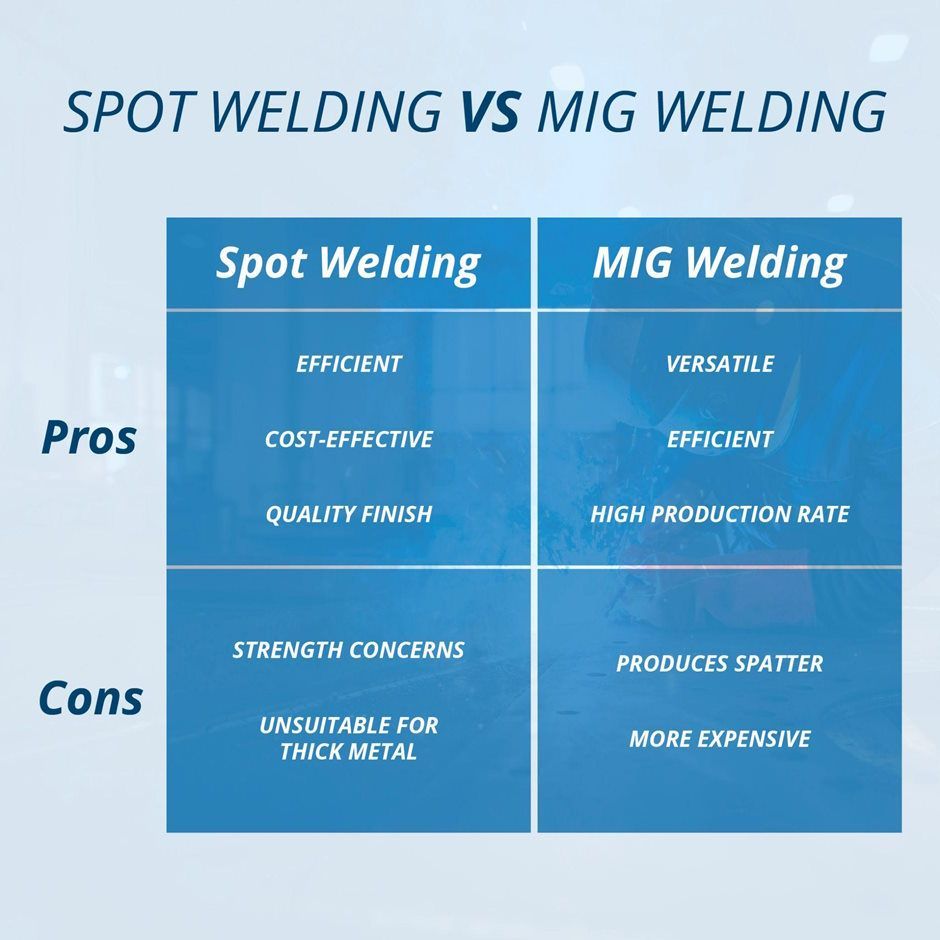
In the realm of metal fabrication and assembly, welding techniques play a crucial role in joining and shaping metal components. Two prominent welding processes that stand out are spot welding and MIG (Metal Inert Gas) welding. Each method possesses distinct characteristics, advantages and applications.
In this article, we’ll delve into both these welding types. We’ll explore the fundamentals of each process, their applications and their respective strengths and weaknesses. Whether you're a seasoned welder or just starting out, this comprehensive guide will shed light on the differences between these two essential welding techniques.
What is Spot Welding?
Spot welding refers to a type of resistance welding technique. It uses a combination of heat and pressure to join two or more pieces of metal together.
The process involves the use of two copper alloy electrodes, which are clamped against the metal pieces being joined together; an electric current passes through the electrodes, which causes the metal pieces to heat up respectively and melt, thus fusing together. Once the current is turned off, the pressure remains, ensuring the molten metal solidifies into a joint.
Applications
When it comes to applications of spot welding, it’s an especially ideal method for manufacturing processes that require parts made of thin metal sheets.
Due to its speed and efficiency, it’s often and predominantly used in mass production across various industries. These industries include
● Automotive: This welding technique is the main joining process used in the construction of steel cars, being used to assemble the car body and chassis.
● Construction: Spot welding is often used in the construction of the building materials, machinery and construction equipment that are used by the construction industry.
● Manufacturing: In manufacturing, spot welding is used in the fabrication of various items, including appliances, electronics and metal furniture.
Other applications include in the shipbuilding and marine industry, in custom metal fabrication, and in the aerospace industry for sheet metal components.
What is MIG Welding?
Metal Inert Gas welding - more commonly referred to as simply MIG welding - is a welding technique that uses an electric arc, created by a constant voltage supply, and a solid wire electrode.
The wire electrode is fed through a welding gun and is continuously fed into the weld area. The electric arc then melts both this filler wire and the base metal, with the two then fusing together. In order to protect the molten weld pool against contamination from atmospheric gases (like oxygen or nitrogen), a shielding gas (an inert or semi-inert gas, such as argon or helium) is also fed through the welding gun.
This process is relatively straightforward to learn and is often used to weld a variety of different metals.
Applications
MIG welding can be used to weld a wide range of metals with varying levels of thickness, which, combined with its speed and affordability, makes it a popular welding choice for many different applications.
Some of its common applications include:
● Automotive Repairs: Motorbikes, cars and other vehicles are often assembled and repaired using MIG welding.
● Sheet Metal: Due to its ability to handle thin metals, this technique is often used for welding sheet metal.
● Construction: MIG welding is used for heavy constructions, such as the creation of bridges, pipelines and building materials.
● Metal Fabrications: MIG welding is commonly used for heavy duty fabrication projects, such as pressure vessels, steel structures and metal gates.
Overall, the process is versatile, cost-effective and semi-automatic, and the welding torch itself is light to use, making it a popular choice for automation and mechanisation.
Pros & Cons of Spot Welding
Pros
Efficient
Spot welding is known to be a fast and efficient welding process, hence why its use is so popular in mass production. The reason it’s such a fast process is because it delivers a large amount of electrical current to a small area in a short amount of time, which also makes it highly accurate.
Cost-Effective
Minimal supplies are needed for spot welding compared to other welding techniques. For example, it doesn’t require the need of any filler metals or shielding gases, which reduces material costs, and can be easily automated, which reduces labor costs.
On top of this, its speed efficiency also reduces production time. All of these things combined makes spot welding a low-cost process.
Quality
The results of spot welding tend to be highly precise, producing consistently uniform joints each time. The localised welds it creates usually produces minimal to no distortion, which also means that post-weld cleaning or finishing is often not required.
Cons
Strength Considerations
Because spot welding only creates a localised bond at the surface of the metal, the joint penetration is limited, making it considerably weaker than some other welding techniques, such as MIG welding. As such, this limits the types of metals it can weld.
Not Suitable for Thick Metal
Spot welding is not a suitable method to use for thicker metals, once again because it only bonds the surface of the metal.
Not only that, but the heat generated during the process easily dissipates into the surrounding material of thick metals, preventing proper fusion from taking place and creating a weak weld.
Pros & Cons of MIG Welding
Pros
Versatility
MIG welding can weld a variety of metals in all sorts of thickness, including steel, stainless steel and aluminium to name a few. It can even be used on dissimilar metals, making it a suitable technique for a wide range of applications and industries.
It’s also adaptable to different welding positions, such as flat, horizontal and overhead.
Efficiency
Like spot welding, MIG welding is also considered highly efficient. This is because of its continuous wire feed mechanism, which supplies a constant heat source and enables fast, uninterrupted welding with minimal stopping and starting.
High Production Rate
MIG welding produces smooth and clean welds that don't need additional sanding or finishing to remove slag or debris. Additionally, it maintains a steady production pace by not requiring frequent rod changes, which minimises downtime.
These two factors combined result in a high production rate.
Cons
Produces Spatter
Though it tends to generate less than some other weld techniques, MIG welding can sometimes produce spatter, which is droplets of hot material (either molten metal or non-metals) that splashes from the weld. This can land on the workbench, floor or general surrounding area from where the welding takes place.
More Expensive
Compared to spot welding, MIG welding can be more expensive. This is because the welding machines used can be expensive to buy, with the need to buy and replace the consumable wire and the inert gas required, further adding to material costs.
Specialist Welding Services
If you’re in need of specialist welding and metal assembly solutions, then you can rely on us here at Cotmor Tool and Presswork.
With our key services including spot welding, MIG welding, metal fabrications and metal assemblies, our in-house capabilities eliminate the need for additional subcontracting, saving you time, reducing costs and ensuring you’re receiving the highest quality standards throughout the process.
Regardless of whether you would benefit from spot or MIG welding for your project, we’re here to meet your requirements. Get in touch with us today to discuss how we can support you.