Aluminium Pressings vs. Steel Pressings: A Comparative Analysis
Precision metal pressing is a crucial process across industries, shaping metals into parts that serve everything from the automotive to construction sectors. Among the many materials used, aluminium pressings and stainless steel pressings are two of the most common options. But how do they compare, and which is best suited for your needs?
This article from the team here at Cotmor Tool & Presswork will outline what pressings are, provide insights into the benefits and limitations of aluminium and steel pressings, and explore when you might consider alternatives like copper pressings or deep-drawn presswork.
What Is Precision Metal Pressing?
Metal pressing, or presswork, involves shaping metal sheets or blanks into specific forms using high-pressure machinery. This can range from simple components to highly complex parts required in sectors such as automotive, aerospace, electronics, and construction. Processes like deep-drawn presswork are often used to achieve intricate, seamless shapes for components like casings and enclosures.
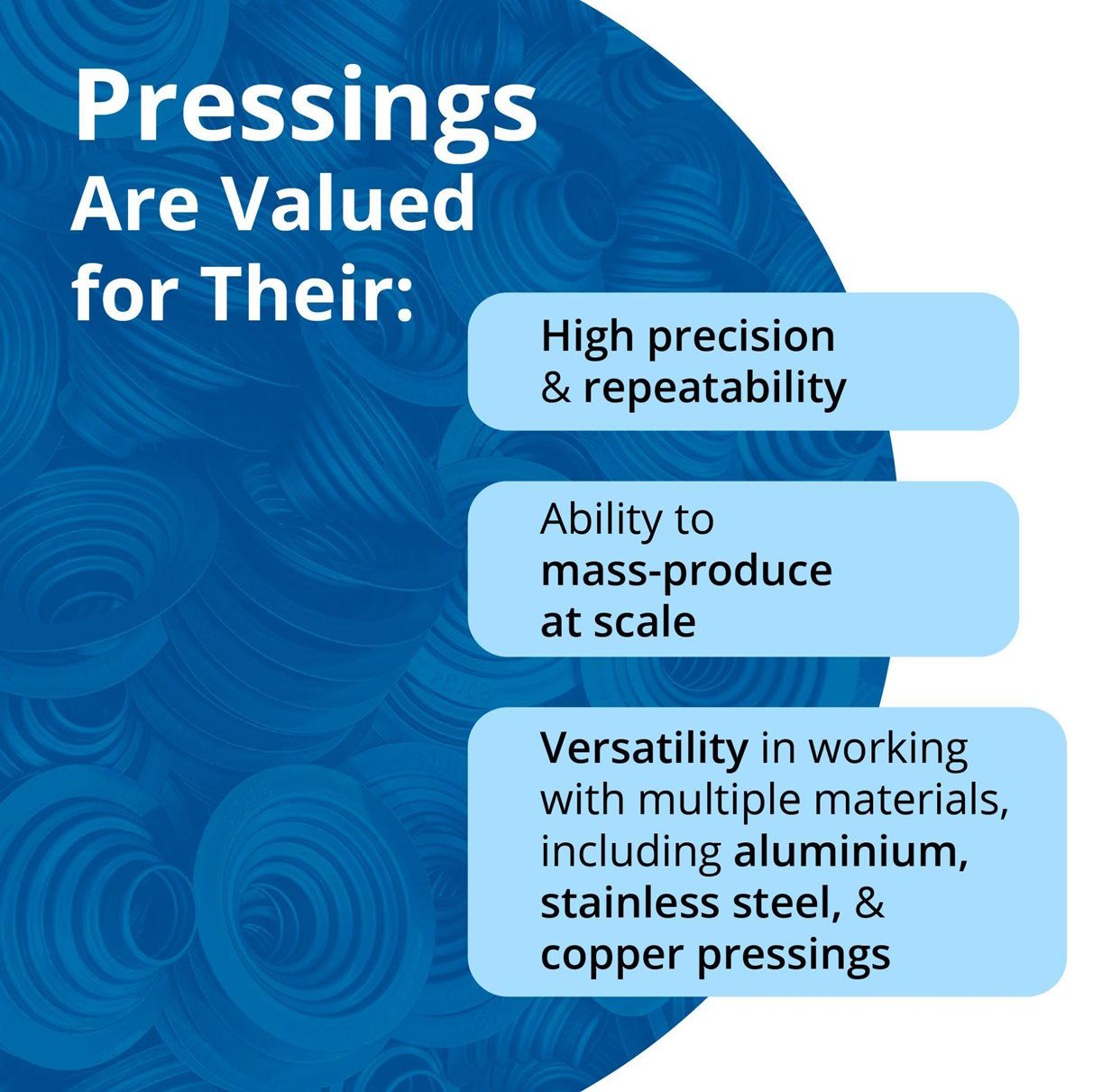
Now, let’s explore the strengths and weaknesses of aluminium and steel when used in precision metal pressing.
Aluminium Pressings: Pros and Cons
Aluminium is a lightweight, malleable, and corrosion-resistant material that is widely used for metal pressing.
Advantages of Aluminium Pressings
Aluminium is approximately one-third the weight of steel, making it ideal for industries where weight reduction is critical, such as automotive and aerospace. It is also corrosion resistant, and naturally forms a protective oxide layer, offering resistance to rust and corrosion without additional treatment.
Its flexibility and malleability allow aluminium to be shaped more easily than steel, particularly for intricate or deep-drawn presswork applications and it also has excellent heat conductivity, making it suitable for applications like heat sinks and electrical enclosures. Finally while aluminium can be more expensive initially, its lightweight nature can reduce manufacturing and transport costs in the long run.
Disadvantages of Aluminium Pressings
Compared to steel, aluminium has a lower tensile strength, which may not be suitable for applications requiring heavy-duty durability. Aluminium is also softer than steel and can be prone to dents, scratches, and deformation under significant pressure.
Best Applications for Aluminium Pressings
● Automotive components to reduce vehicle weight
● Aerospace parts where the strength-to-weight ratio is critical
● Electronics, including casings and heat-dissipation components
Steel Pressings: Pros and Cons
Stainless steel and carbon steel remain the go-to choices for industries demanding robust, durable components.
Advantages of Steel Pressings
Steel, especially stainless steel pressings, offers superior tensile strength, durability and wear resistance, making it ideal for heavy-duty applications. It is typically more affordable than aluminium, particularly for lower-volume projects and retains its structural integrity under high temperatures, offering better performance in demanding environments.
Steel comes in various forms, such as stainless steel, carbon steel, and galvanised steel, providing versatility for different projects. And finally, steel is highly recyclable, aligning with sustainability goals for industries focused on reducing waste.
Disadvantages of Steel Pressings
Steel is significantly heavier than aluminium, which can limit its suitability in industries requiring weight reduction and while stainless steel is corrosion-resistant, untreated steel requires protective coatings to prevent rust and oxidation. Steel is also less malleable than aluminium, making it more challenging to work with for intricate or deep-drawn presswork designs.
Best Applications for Steel Pressings
● Construction components where durability is critical
● Industrial machinery and tools
● Heavy-duty automotive parts, such as suspension systems and engine components
Comparing Aluminium and Steel for Pressings
When deciding between aluminium pressings and steel pressings, several key factors come into play:
● Weight Vs. Strength
● Cost
● Corrosion Resistance
● Complexity Of Design
● Industry Applications
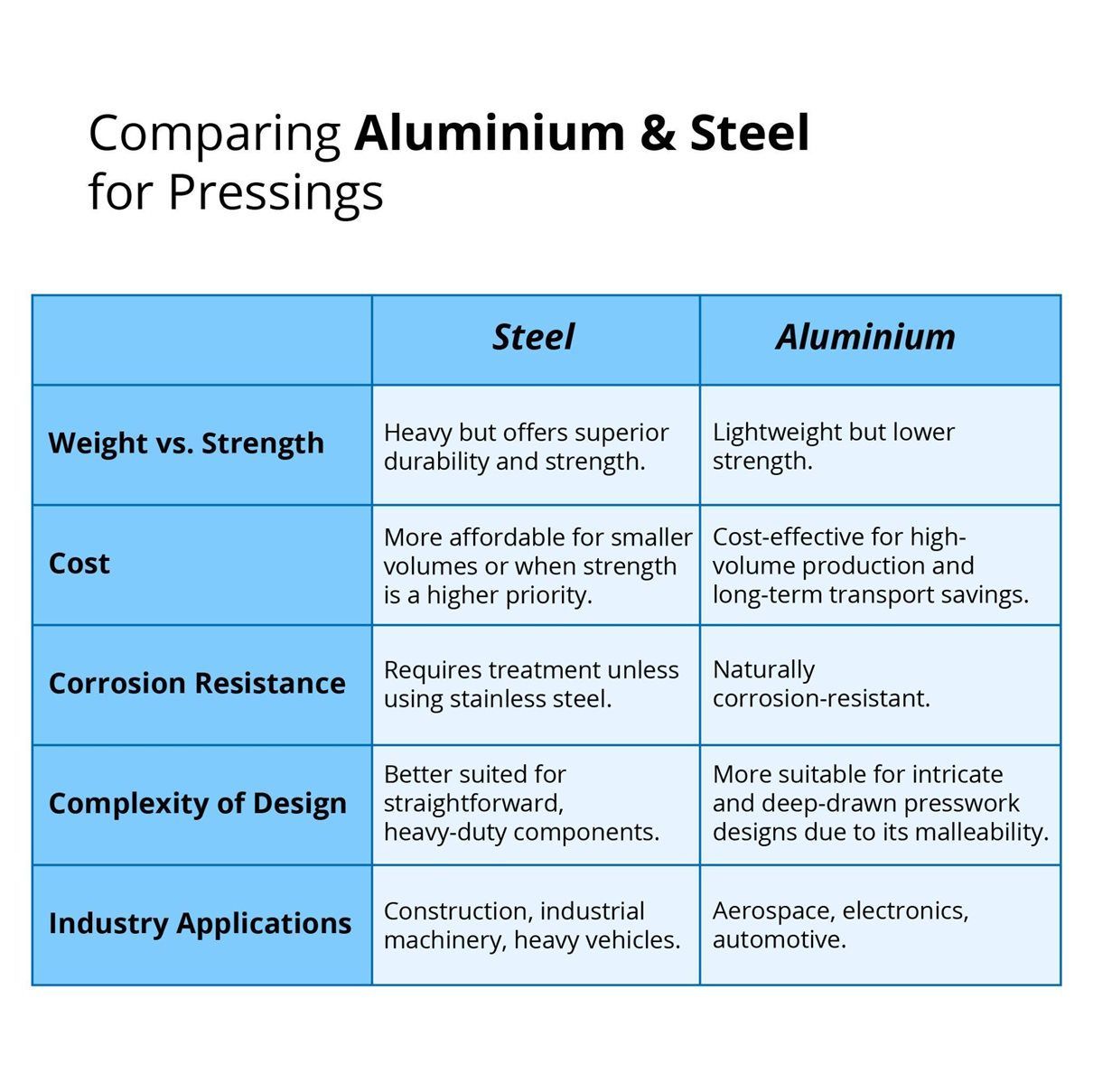
Considering Alternatives: Copper Pressings and Deep Drawn Presswork
While aluminium and steel are dominant in precision metal pressing, materials like copper are also worth considering for specialised applications.
Copper Pressings
Copper is renowned for its conductivity and durability, making it ideal for electrical components, plumbing fixtures, and decorative parts. Key benefits include:
● Excellent thermal and electrical conductivity
● High resistance to corrosion
● Aesthetically appealing for architectural pressings
However, copper can be more expensive than both aluminium and steel, and its weight is closer to steel.
Deep Drawn Presswork
When designs require seamless, complex shapes, deep-drawn presswork excels. This process involves pulling a metal blank into a die to create parts with a consistent, thin-walled profile. Both aluminium and steel can be used in deep drawing, with aluminium offering better malleability for intricate designs and steel providing durability for industrial-grade parts.
Precision Metal Pressing From Cotmor Tool & Presswork
The choice between aluminium pressings and steel pressings ultimately depends on the specific demands of your project. Aluminium is the best choice for lightweight, corrosion-resistant applications where malleability and long-term cost savings are essential.
Steel is ideal for projects that prioritise strength, durability, and cost-effectiveness in smaller volumes. For specialised needs, materials like copper pressings or processes like deep-drawn presswork can deliver tailored solutions.
Established in 1953, the team here at Cotmor Tool & Presswork are proud to offer a range of metal pressing, welding and lamination services - with a customer base reaching from our base in the West Midlands to customers in Europe, Brazil and even China.
We are able to offer our services to a range of industries, such as electrical engineering, commercial vehicles, agricultural machinery and much more, developing our skills and equipment over the years to be able to offer both high-volume production and short runs.
If you’d like to find out more about how we can help with your metal pressing needs, feel free to get in touch with us today.